Movement
For hundreds of years, people who buy gear of any sort lived by restoring and repairing their gear when it broke down and reuse them again. They were also allowed to sell off used gear to those who could not afford newly minted work tools or stuff they needed to get by.
A support economy of repair jobs and tinkers help people sustain their lives by allowing for the restoration of work tool functionality and keeping gear useful. Not much resources are lost when society is allowed to fix what they buy and to sell second-hand gear to those who cannot afford or wait for craftsmen to mint brand new tools.
Image Credit: MikroLogika for Wiki Commons CC BY-SA 3.0Scrap mobile phones that can be sourced for parts.
People are able to sustain their means of making a living and make their lives easier via a repair economy.
Even in the modern age, from vacuum tube electronics to the first generation integrated circuit boards, a fair repair opportunity existed and people were even able to prolong the usability of old tools by jury-rigging parts together to keep a product functional and useful for everyone.
In the past two decades or so, starting with software, companies started including preventive repair measures for their products and services.
At first this was intended to keep owners from doing unintended harm to what they owned if they weren't qualified to technically tinker with their gear.
Then, as manufacturers figured out that the repair cycle of their product lines could also bring in revenue, brands created a situation where repair would cost a premium and customers would be forced to either buy a new product upgrade from them or pay a service contract to keep a newly purchased item functioning normally with technical support. These new contrivances and conditions cost the consumer extra--and consequently earning more revenue for brands.
Image Credit: repair.org websiteBuyers of new gadgets today and generations of repair people who fix stuff for a living are now unable to deal with even simple breakdown problems because they don't have access to a product's repair manual or spare parts. Most of the time, when a new gadget gets bricked, It's just more convenient to buy a new product from the same manufacturer.
In spite of this, a growing movement of consumer advocates, repair professionals and ordinary individuals are working to push for legislation that would make it harder for companies to keep repair information proprietary. The U.S. copyright office has already made it known to manufacturers that consumers have a basic right to fix their own vehicles such as tractors and cars, as well as electronic tablet computers in a 2015 ruling on copyright coverage of fair repair allowed under the law.
Planned Obsolescence
Designing products to be less useful in the long run has long been a marketing trick by manufacturers in order to force consumers to always be looking to get the supposed better product. This has been documented since the 1940s by consumerist groups studying brand manufacturers.
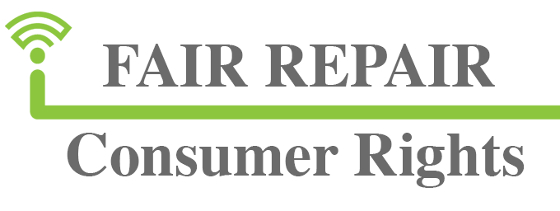
Why Are Brands Keeping People from Repairing what They Buy?
Brand companies also use “repair prevention” as a method for preventing their trade secrets from being compromised but have been creating a usurious environment where defective products force gadget users to buy new stuff, pay for exorbitant service contracts, or penalize resellers of used software.
Restrictions that prevent consumers from having the products they own fixed anywhere besides a licensed repair shop force people to either pay to keep using an old product or junk their gadget and go out and buy a new one.
Once repair is an exclusive right of the manufacturer and old model products are no longer supported, consumers who continue to use old products from hardware to software become vulnerable to breakdowns and often have no recourse. Replacing good products that can still be repaired creates a wasteful resource economy.
The vicious cycle already forces plenty of enterprise techs and engineers to adopt an open source worktool and economy environment. One where people are now allowed to build their own gear for a lower cost and with shared knowledge instead or protprietary patents and copyrights. But the open source tools and gear have the same quality and effective use as brand products. Sharing knowledge is now essential for a sustainable future and repair knowledge is part of that future.
Kyle Wiens of iFixit wrote an article for The Guardian where he expressed concern about the repair prevention tactics of manufacturing companies:"My company iFixit,
a free repair manual for everything, has dodged copyright entanglements
by taking apart products, writing our own guides from scratch and
posting them online for free..."
"Let me make one thing clear: copyrighting repair manuals doesn't
protect creative work and it doesn't prevent knock-off artists from
copying design..."
"All it does is stop people from fixing their things. It
prevents independent repair facilities and shops from having the
information they need to repair your stuff at competitive prices. And it
prevents refurbishers from having the resources they require to fix
products and put them back on the market."
Windfall Recycle and Job Industries Create Sustainability
Several groups have already taken it upon themselves to create a repair economy in their local communities, from regional repair groups to online repair communities to bypass the oppressive no-repair or exclusive repair policies of brands.
- In Minneapolis, a nonprofit called Tech Dump provides electronic recycling and refurbishment, employing workers not considered traditionally employable, many of whom have criminal records. The low prices of the organization's refurbished items allow people who might not be able to afford, say, a new computer purchase a good-condition laptop.
- iFixit, is a website that provides repair instructions and
DIY advice and tools, approaches the problem from a different angle: if
companies won’t provide us with the information to fix our own products,
we’ll figure it out ourselves. The site functions as a sort of repair
Wiki, with some one million users sharing knowledge.
Sleek Bricks? Or Clunky Stuff that Can Be Fixed?
Form factor and technology has been a bane unto itself for creating products that look sleeker or more ergonomic at the expense of repairability. Micro-miniaturized electronics that use rare-earth metals and composite materials require specialized tools and techniques that are simply out of reach of the average technician.
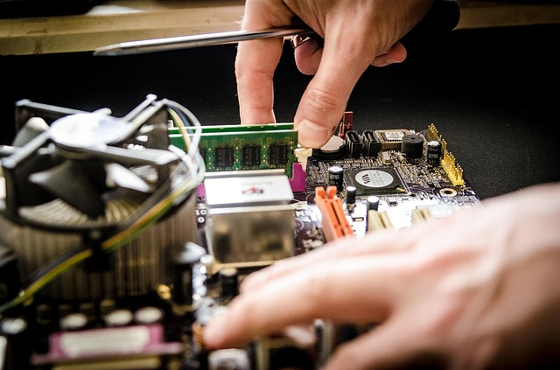
The smaller and flatter your mobile phone, chances are it will be a brick if something goes wrong with it, no matter how cool it looks. No should really can brag about a $500 and up fully-featured smart phone that turns into junk under normal wear and tear in just 6 months or even for 2 years. If the repair movement is to prosper, manufacturers should rethink their design philosophy to sell items that can be used forever and be easy to upgrade via modular add-ons as simple as a SIM card plug-in.
The same for flatscreen TVs and HD widescreen theater TVs that can be redesigned as easier to repair and upgrade. Even mobile phones and smartphones are designed with proprietary parts (Apple designed a unique screw for their iPhone just so they could not be repaired by anyone) that prevent easy access and repair by DIY and professional repair technicians. Basic parts like batteries are sometimes proprietary so you can only get replacements from the brand.
Tech skills like digital logic analysis and an understanding of the software to analyze it are specialized repair expertise that cost a lot so brands prefer to have everything performed in-house.
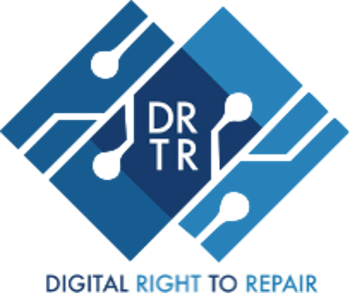
These days product life cycles are too short and you still pay for support whether you need it or not. Service contracts are now a significant part of every smartphone purchase and this should be something a local DIY repair man can do if repair manuals were available to everyone.
It may not even be economical for manufacturers to provide reasonable repair services for high-end smartphone and tablet computers and when one does conk out, it almost never runs the same way as when brand new even if repaired by the brand. In cases where repairs are possible on high-end electronics, any damage compromises the gadget's reliability. Some products are even manufactured without a repair loop built in. If it works, it works well, but if it starts to conk out or become wonky, it's as good as scrap.
Image Credit: repair.org websiteThe repair movement in the U.S. is pushing for legislation to put consumer rights into law in each state that allows fair repair policies and buyer freedom for tinkering and reconfiguring what they purchase as well as reseller rights for product owners.
If you are a manufacturer of any product, designing easy repair as a feature of your product should be a unique selling point that should work in your favor. It may be a life skill for everyone to learn basic repairs of stuff they own and use or provide active support to your local repair tech community to keep eveything everyone owns useful for as long as possible.